What if your scrap could help decarbonize advanced manufacturing?
A new independent study conducted by researchers at Oregon State University has confirmed just how impactful recycled materials can be when paired with the right technology. The Life Cycle Assessment (LCA) of nickel powder production found that Continuum Powders’ Greyhound M2P plasma atomization process cuts carbon emissions by up to 99.7% compared to traditional virgin nickel powder production.
Download Full Study
A Better Way to Make Metal Powders
Nickel powder is a critical material in high-performance industries like aerospace, energy, and defense. But traditionally, producing it requires mining, refining, and multiple remelting steps—all of which come with significant environmental costs.
Other powder producers often rely on pre-alloyed ingots or wire feedstock that require energy-intensive processing before they can be atomized into powder.
Continuum’s process is different.
Using its patented Greyhound M2P technology, Continuum directly converts 100% scrap metal into ASTM-grade powder. No remelting. No chemistry adjustment. Just high-purity, high-performance powders made from material that would otherwise be discarded.
What the Study Showed
The research, led by Oregon State University’s Industrial Sustainability Laboratory, compared three different production scenarios:
- Conventional production using 100% virgin nickel
- A hybrid approach using partially recycled feedstock
- Continuum’s method, using 100% scrap feedstock and M2P technology
The findings? The conventional method contributed to 96% of the total carbon emissions across the nickel powder production process. Continuum’s approach reduced that by 99.7%—a game-changing difference.
“This study confirms what we’ve known—sustainable metal powder production is not just an aspiration; it’s a reality,” said Sunil Badwe, Ph.D., CTO of Continuum Powders. “By transitioning from virgin to recycled metal feedstocks, we’re proving that sustainability and high-performance manufacturing can go hand in hand. The results of this LCA study validate our commitment to reducing emissions while delivering high-quality powder solutions.”
Academic Validation from Oregon State University
The OSU research team not only conducted the LCA but also recognized the broader importance of the findings.
“Our findings demonstrate how focused and thoughtful development of advanced technologies and use of industry best practices can improve the sustainability profile of products we use every day,” said Karl Haapala, Ph.D., Professor of Advanced Manufacturing at Oregon State University.
Fellow researcher Kamyar Raoufi, Ph.D., a postdoctoral scholar, added, “Continuum Powders’ approach represents a tangible step toward a more circular and sustainable manufacturing economy.”
Why This Matters
As global industries face mounting pressure to decarbonize, Continuum’s approach offers a scalable, near-zero carbon solution for sourcing critical metal powders—without sacrificing quality or performance.
For manufacturers focused on ESG goals, cost savings, and supply chain security, this LCA-backed process offers an undeniable edge.
Want to dive deeper? Download the full study today!
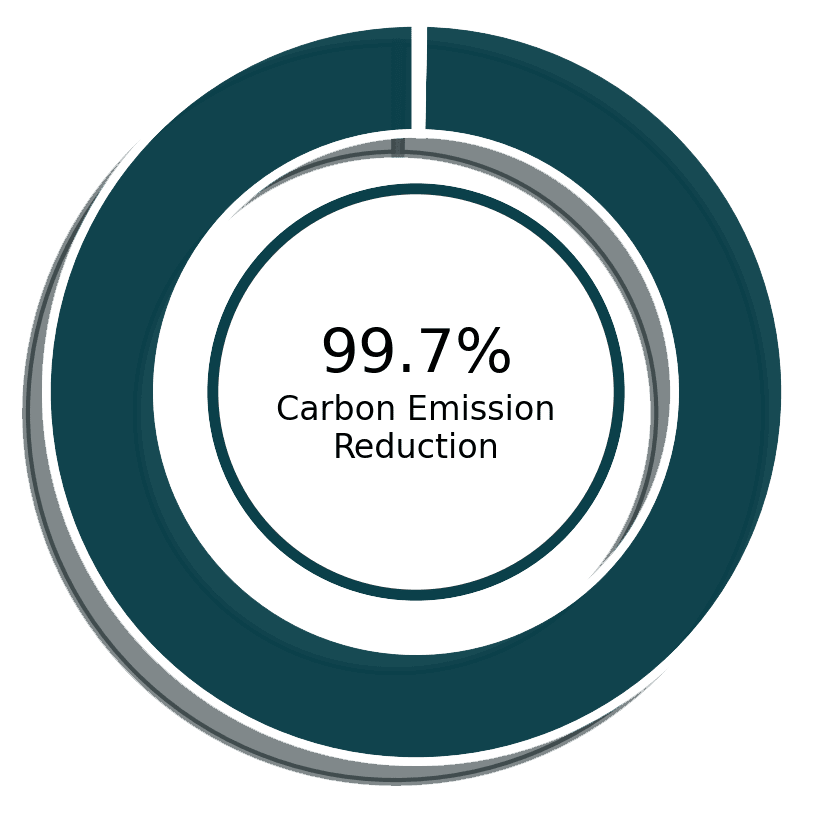